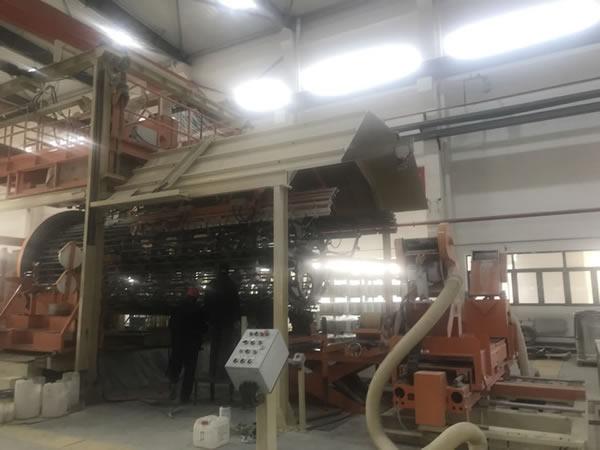
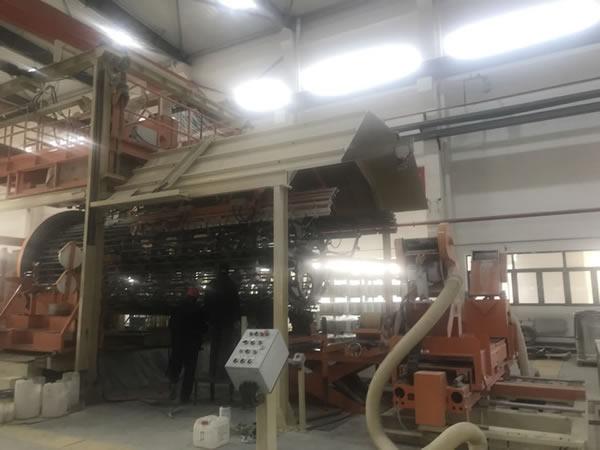
CFW Pipe Winding Machine
Telephone Bargaining
CFW continuous filament winding pipe winding machine
Equipment technical parameters and working principle
CFW3000 continuous pipe winding machine
Continuous pipe winding machine function: It is the main equipment of GRP pipe production line used for GRP pipe production. The mechanism and working principle are as follows: it mainly consists of main shaft transmission device, overall frame, steel belt propulsion device, aluminum beam fixed plate and steel belt circulation head, steel belt circulation guiding roller, steel belt support aluminum beam, steel belt, inner liner cutting yarn device, structural layer cutting yarn device, sanding device, inner liner cutting yarn creel, structural layer cutting yarn creel, structure layer winding yarn creel, inner liner resin stirring and dispensing device, structural layer resin stirring and dispensing device, infrared heating system, winding polyester film frame, winding surfacing veil frame, winding outer protective layer frame, inner liner pneumatic pressure roller, structural layer pneumatic pressure roller, complete pneumatic pressure roller, hydraulic lifting platform, online cutting, trimming device and dust collecting device, PLC control system and electrical control system.
The mold consisting of aluminum beam, fixed plate, steel belt circulation guiding roller, steel belt circulation head, steel belt support aluminum beam and closed-loop steel belt, shall be installed on the main drive of the winding machine.
When the main shaft of the winding machine rotates under the push of the propeller, the steel strip will be wound around the aluminum beam distributed along the fixed disc. At the same time, under the action of the steel strip propulsion device, the steel belt moves along the winding main axis, and when the main shaft rotates a circle, the steel belt propulsion device advances the steel strip axially by a strip width. When the steel strip is advanced in the axial direction to the tail end of the aluminum beam, the steel strip enters the steel strip circulation guiding roller and the steel strip circulation head, and the steel strip is introduced into the winding main shaft (hollow shaft) to return to the starting point of the winding. In this way, the steel strip forms a winding, advancing, deriving, introducing, rewinding cycle.
When the steel strip is formed into a winding cycle, a layer of polyester film and a surfacing veil are wound on the steel strip. At the same time, the upper lining resin leaching device and the structural layer leaching device are used to pour the resin onto the steel strip. The inner liner cutting yarn device and the structural layer cutting yarn device cut the fiber yarn onto the steel belt. The sanding device adds quartz sand to the steel belt, and the winding creel provides the entangled fiber yarn. When the steel fiber, resin, quartz sand is fully mixed and soaked under the action of the rolling device. Under the action of the steel strip, it advances along the axial direction of the main shaft into the infrared heating zone, and performs heating and curing while continuing along the axial direction of the main shaft and leaving the steel strip mold. The hydraulic lifting platform is raised in order, and the roller on the platform is lifted to cure the pipeline. After the pipeline has a certain length, the cutting is performed on the line, the trimming device starts to cut the pipeline and the pipe ends are trimmed. Thereby, the pipe making is completed, the amount of the cut yarn, the amount of the cut yarn of the structural layer, the amount of the wound yarn, the amount of the quartz sand, and the amount of the resin are preset and controlled by the PLC. The resin temperature and quartz sand temperature are also controlled by the PLC.
Industry Category | Machinery/Machine-Tools/Other-Machine-Tools |
---|---|
Product Category | |
Brand: | |
Spec: | |
Stock: | |
Origin: |